3D printing is one of the newest and most influential up-and-coming technologies. This revolutionary technology has completely transformed and enhanced filmmaking. But what is 3D printing? 3D printing is the process of making a physical object from a 3D digital render by laying down multiple layers. It has already been integrated into filmmaking in various ways including sets, props, costumes, character prosthetics, and in some cases animation. The possibilities are endless in the world of film production with this new tech.
Claymation/ Puppetry
Puppetry is one of the original forms of entertainment dating back to as late as 5th century BC. It has come an extremely long way since then. Jim Henson’s Creature Shop is a special/visual effects company that has built puppets for iconic shows such as Fraggle Rock and The Muppets. They have taken advantage of this new technology to improve puppetry in their shows. I spoke to Brooke Eldridge who has had first-hand experience on the sets of these shows and she said “Our arm rods at Sesame are 3D printed, where they used to be made of wood. 3D printing ensures a faster and cheaper process than wood carving while still being light. The doozers on the new Fraggle Rock series, all their gear and clothes are 3D printed too.” Previously Fraggle Rock Doozers were sculpted from scratch using silicon and plaster molds which was time-consuming and costly. The use of 3D printing these puppets has provided so many benefits. No longer does it take days and tons of material to create one character but it now can take as little as a few hours and some plastic. 3D printing the Doozers has also almost cut in half the speed it takes for a character to complete an action with its hands in a scene. Doozers hands are 3D printed with magnets inside of them so they can quickly be changed in seconds for a scene.
Puppets have historically been operated by a person’s hands but people have adapted to use mechatronics in these puppets which have been named animatronics. Lots of film companies use mechatronics in their puppets to make them move more fluently and smoothly. To custom make the skeletal face and parts of these animatronics it can be costly and give the puppet a lot of weight. 3D printing allows these parts to be produced at half the price and nearly half the weight.
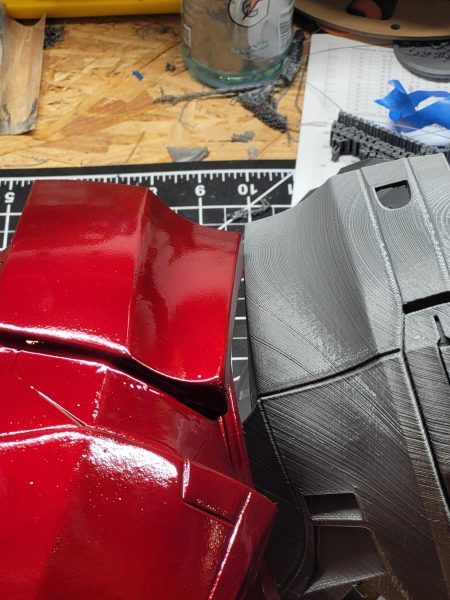
Claymation is “ one of many forms of stop-motion animation . Each animated piece, either character or background, is “deformable”—made of a malleable substance, usually plasticine clay.” One of the largest claymation studios is Laika Studios they are best known for movies such as Coraline, Paranorman, BoxTrolls, and Kubo to name a few. In the past claymation was an extremely difficult and tedious art. The process of shooting one conversation between characters could require a sculpture to create hundreds of facial expressions. Typically these expressions were sculpted by hand in clay which could take days and cost a lot of money. These clay characters can be extremely miniature requiring the sculpture to have the utmost precision in their details. To combat this very difficult process many companies like Laika Studios have evolved to incorporate 3D printing when creating characters. Now, a designer can model a character digitally and print out hundreds of facial expressions in hours. This also allows more consistency in the characters’ expression in contrast to the unpredictability of a person sculpting it by hand to a computer programmed to do an exact command. 3D printing can give studios more flexibility in the beginning stages of their production. When designing the concepts for a character the studio can go through more trial and error without spending that much money or time. They can print out a character, run it through a screen test, and adjust the scale at a revolutionary pace.
Props
The part of filmmaking that has benefited most from 3D printing is prop making. It has opened up so many capabilities and completely expanded the horizons of what props people can make for films. I was given the opportunity to get some words from Peter Allen, a production assistant at Warner Brothers he said “From the experiences I’ve had so far in the industry, it seems like 3D printing has opened up a multitude of new pathways for costuming and set decor specifically. Specifically in the indie space the use of 3D materials allows creatives who are working in confined budgets to still reach their potential of the project they are working on. With the cost of the basic material being so cheap a single person with the knowledge of 3D printing is now able to create objects and props that only 20 years ago would have taken many more man hours and significantly more money spent. In short, it has created a wonderful new avenue that really allows smaller productions to be able fully express their vision on screen.” 3D printing has given us the ability to create things we have never imagined. We now have the access to create props that never existed before or that are no longer sold with less cost. For example, a gun from WW2 that no longer is in production that would cost hundreds of dollars to buy or replicate can be printed out in exact detail for pennies to a dollar. Even props that never existed like a futuristic ray gun can be modeled and printed out. The best part is if the production has a printer on site they can get the prop as early as the next day which saves the crew valuable time. If the prop is made and is too small or too big it can be quickly adjusted and printed again. There are many instances where an actor needs to break a prop in a scene and it takes many scenes to capture the right shot. Instead of having to buy duplicates of the prop it can be 3D printed as many times as needed to be broken. Even if a prop is broken by accident it can be replicated easily.
Costumes
Costumes in film are an art in itself but they can be really difficult to create like any form of art. One of the most daunting tasks is fitting an actor for their costume. Typically the actor has to get a silicon cast of their body if they need to be custom fit for something like armour and they can’t be there all the time to try it on. Silicon casting can cause lots of product waste. With newer technologies an actor can be scanned in a full-body 3D scanner in minutes then their body can be 3D printed as a custom mannequin to test fit costumes on. These mannequins serve as accurate models for testing costumes, eliminating the waste that traditionally comes with silicon models. 3D printing can also be used to make tons of different armor in a similar way in which it’s used to make props. In the past Marvel studios painstakingly sculpted pounds of clay into prototype armor for the Ironman movies. Now they can more easily print a piece of armor out and scale it to the 3D model of the actor.
This new technology provides the opportunity for rapid prototyping and precise customization, it has not only saved productions valuable time and money but has also opened up new creative possibilities. As filmmakers continue to explore its potential, the future holds even greater advancements in cinema by the boundless and ever evolving possibilities of 3D printing.